INVENTION Russian Federation Patent RU2232710

HYDROGEN GENERATOR
Name of the inventor: Cheliabinsk VF (RU); Deaf IN (RU); Scherbakov AN (RU) The name of the patentee: Open Joint Stock Company "Rocket and Space Corporation" Energia ". SP Korolev" (RU) Address for correspondence: 141070, Moscow region, Korolev, st.. Lenin, 4a, OAO RSC "Energia". SP Queen "Industrial Property and Innovation Department, A.G.Sakoyanu Starting date of the patent: 2003.04.14
The invention relates to power equipment and can be used to produce hydrogen in stationary installation or transport. The hydrogen generator, running through the hydrolysis of the solid reactant - aluminum, has a reaction vessel supply pipe aqueous sodium hydroxide solution, hydrogen dispensing line. The hydrogen generator has a container with a solid reagent - aluminum heat exchanger for removal of reaction heat, made of metal resistant to the action of an aqueous sodium hydroxide solution are placed inside the reaction vessel filled with an aqueous solution of sodium hydroxide and having a direct thermal contact with the solid reactant - aluminum. Thus the metal from which the heat exchanger has a higher thermal conductivity than the solid reactant - aluminum. The invention allows to intensify the process of hydrogen generation.
DESCRIPTION OF THE INVENTION
The invention relates to power equipment, and can be used to produce hydrogen in stationary installations and transportation.
The generator is a chemical reactor that produces hydrogen by hydrolysis, i.e. decomposition of water. For this purpose, the solid reactant, ie, hydrolysis reaction is heterogeneous in nature - is on the surface of a solid. It is assumed that the hydrogen thus obtained is then used as a fuel for power plants (EI) of the fuel cell (FC). Additionally, hydrogen can be used, of course, in other areas, such as in metal cutting, welding, etc.
Previously, the latter was used mostly acetylene, which was synthesized in generators having a similar structure [1]. Thus both heterogeneous hydrolysis reaction used, and as the solid reactant served calcium carbide. This technical solution is taken as equivalent. Its disadvantages include the following:
- Synthesized acetylene is not suitable for kislorodovodorodnyh TE and needs further decomposition to produce hydrogen; This significantly complicates the design of power plants and reduces its efficiency; low weight the hydrogen content of such oscillators makes them unsuitable for transport;
- Insoluble residue (lime) is formed by the acetylene generators, which limits the accumulation of time, not continuous operation of the generator, it worsens its dimensions and weight characteristics; removal of sludge from the reactor requires additional energy costs, complicates the construction of power plants, reduces its efficiency;
- Solid reagent (calcium carbide) is a material long-term storage which is quite difficult and unsafe, because it is very hygroscopic, and upon absorption of moisture from the air releases acetylene.
Closer is essentially a hydrogen generator for power plants based on fuel cell power used on submersible [2]. The reactor and the hydrolysis reaction uses, as a solid reactant metal hydrides are used (i.e. metal compounds with hydrogen). The generator includes a reaction vessel into which the "camera" with a metal hydride, a heat exchanger for removing heat of reaction, water mixing device to the reaction vessel (placed inside the latter) and a line for supplying water from the reactor and hydrogen removal reactor. At the same time to improve the dimensions and weight characteristics of PP are used light metal hydrides, which are quite expensive (LiH, BeH 2 ...). This significantly increases the cost of producing hydrogen and is a significant drawback of the generator [2] adopted in this case for the prototype.
In addition, the disadvantages of the prototype should include the following:
- Used for the hydrolysis of solid reagent is a significant danger of the fire point of view, because the metal hydrides are prone to spontaneous decomposition with evolution of hydrogen and hygroscopic, which leads to their degradation with evolution of hydrogen;
- Metal hydrides are expensive and recovery obtained by the hydrolysis of metal hydrate is technically complex and energy intensive;
- A design flaw is the generator and its inertia, complicating its use in the transport EI.
This is caused by the fact that for the operation of the generator for steady state temperature is necessary to maintain a certain solid and liquid reagents. If a lot of them, maintaining temperature generator technically complicated and requires significant energy consumption (for example, mixing devices for work). Furthermore, transient modes such hydrogen generator in this case take much time because they require large masses temperature change substances having a relatively low thermal conductivity (water, metal hydrides). For transport purposes, this is a huge disadvantage.
The object of the proposed solutions is to provide a hydrogen generator with a high performance. In addition, the generator has to work on the cheap and widespread raw material, storage is safe, and the use of hydrolysis does not give an insoluble precipitate. The problem is solved in that the generator of hydrogen working by hydrolysis of the solid reactant - alumina having a reaction vessel line feeding an aqueous solution of sodium hydroxide, pipe issuing hydrogen introduced container with a solid reagent - aluminum heat exchanger to remove heat of reaction made of metal resistant to an aqueous solution of sodium hydroxide, placed inside the reaction vessel filled with an aqueous solution of sodium hydroxide and having a direct thermal contact with the solid reactant - aluminum, the metal, from which the heat exchanger has a higher thermal conductivity than the solid reactant - aluminum . Thus, as the reagent used for the hydrolysis reaction of aluminum and the aqueous alkaline solution (NaOH); It formed in the reaction liquid alkaline solution of sodium aluminate. The speed of the hydrogen generator is increased due to the intensification of thermal processes in the generator and their localization.
The essence of the proposal is as follows.
Thermal processes in the proposed generator accelerated thanks to the fact that the very solid reactant involved in the hydrolysis of a metal with high thermal conductivity (aluminum) and, in addition, is in direct thermal contact with both the starting heater and a heat exchanger to remove heat of reaction. In addition, the metal from which the heat exchanger is made, and a good conductor of heat. If higher thermal conductivity than the metal-containing reactant (Al), the generator speed is limited only by the thermal conductivity of the reagent. As a material for such a heat exchanger can be used, such as copper, having a larger than that of aluminum, heat conductivity and is resistant to the action of an alkali.
In this heat exchanger, and it is advisable to combine the two functions - the removal of heat of reaction on the stationary generator mode and the influx of heat when the generator is started. Thus, a heat exchanger to remove heat of reaction during start trigger generator may be a heater. At this temperature coolant circulating in the heat exchanger, above the liquid temperature in the generator. Due to the high thermal conductivity of the metal reactant, the metal material of the heat exchanger and a direct contact heat, heating the solid reagent and is thus at an increased rate.
Performance of the proposed reactor is increased and due to the fact that no temperature adjustment is carried out during the entire reaction mixture (as in the prior art), but only near the solid reactant. Since in this case hydrolysis is heterogeneous and the reaction proceeds on the surface of aluminum, there is no need to maintain the temperature at the desired level throughout the reaction mixture. Enough of the aluminum to regulate temperature and a thin layer of liquid near the surface. Thus, localization is carried out controlled thermal processes, ie, It decreases the area in which heat transfer is controlled. Accordingly, the reduced weight of the substance contained in the zone.
Such localized thermal control zones can significantly increase the rate of thermal processes that affect the evolution of hydrogen gas, and hence the performance of the hydrogen generator. The latter is thus increased simultaneously by several factors:
- The use of a solid reagent for the hydrolysis of high thermal conductivity (Al);
- Direct thermal metal reagent contact with starting the heater and the heat exchanger to remove heat of reaction;
- High thermal conductivity of the metal, which is made of a heat exchanger to remove heat of reaction;
- Localization of thermal processes responsible for the generation of hydrogen.
 |
proposed oscillator circuit 1 is illustrated, where indicated:
1 - reaction vessel;
2 - a container with a solid reagent;
3 - solid reactant - aluminum (shown in the form of pellets, but may be used in sheet form, etc.);
4 - liquid reactant feed pipe - aqueous solution of sodium hydroxide (NaOH);
5 - a heat exchanger to remove heat of reaction of aluminum and heating generator during start-up;
6 - backbone hydrogen dispensing.
|
Powered Generator follows. Aluminum (in the form of pellets, sheet, etc.) is placed in a container with solid reactant (2) so that the solid reagent (3), such as aluminum, has direct thermal contact with the heat exchanger (5) for removing the heat of reaction of aluminum and heating when the generator is started. The latter is placed inside the reaction vessel (1). By liquid reactant supply line (4) into the reaction vessel (1) is fed an aqueous alkali solution such as NaOH, so that the container (2) with a solid reagent (aluminum) is immersed into this solution. Exothermic hydrolysis reaction starts and release of hydrogen that is withdrawn via line issuing hydrogen (6). Self-heating of the reagents thus takes place slowly enough, and to accelerate the hydrolysis of the heat exchanger (5) serves a hot water which heats the aluminum and the solution was near him. hydrogen evolution is intensified, and after achieving the necessary heat exchanger flow rate (5) is switched to the removal of heat released in the reaction.
The effectiveness of the proposed measures has been verified experimentally. To do this in the laboratory was made glass small-scale working model of the proposed generator, test the functionality of the proposed device and its performance.
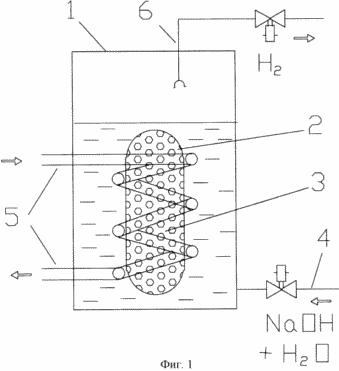 |
Photography generator is given in Figure 2, where the main elements are indicated, and its design. The solution of alkali in the generator is not filled.
Heat exchanger for heat reaction was carried out in the form of a spiral of copper tube, which is fed by the cold water tap. Depending on the performance of the generator temperature therein 40-120ºS varied range. This Hydrogen generator performance determined water flow in the cooling heat exchanger. Direct contact between the heat exchanger and the metal-reagent carried by the fact that the aluminum granules poured directly onto a copper spiral heat exchanger to remove heat of reaction (2). Starting the heater has not been used in the tests, and the generator was started self-heating, which took about 20 minutes.
Experiments have shown that a significant (several times), the generator reduced productivity achieved within 3-10 seconds after changing the water flow in a spiral heat exchanger. Obviously, for such a time that any appreciable change temperature of the liquid in the flask (~ 0.5 L aqueous NaOH solution) is almost impossible, and rapid "response" of the generator for cooling small changes due to the high water flow rate of heat transfer through copper and aluminum and its localization controlled thermal and chemical processes near the surface of the pellets (A1).
|
Thus, this technical solution allows to create a hydrogen generator using hydrolysis cheap common substances which do not form a precipitate resulting solid reaction. This generator design is quite fast, which is important for use in transport.
The efficiency of the proposed structure is confirmed experimentally.
INFORMATION SOURCES
1. VV Rybakov gazosvarshchika textbook. M .: Mashgiz., 1956, p. 32.
2. Hydrogen generation by hydrolysis to power plants based on fuel cells scuba destination. U.S. Patent №5372617, 1994 g.
CLAIM
The hydrogen generator, running through the hydrolysis of the solid reactant - alumina having a reaction vessel line feeding an aqueous sodium hydroxide solution, backbone hydrogen dispensing, characterized in that it comprises a container with a solid reagent - aluminum heat exchanger to remove heat of reaction made of metal, resistant to the action of an aqueous solution of sodium hydroxide, placed inside the reaction vessel filled with an aqueous solution of sodium hydroxide and having a direct thermal contact with the solid reactant - aluminum, the metal, from which the heat exchanger has a higher thermal conductivity than the solid reactant - aluminum.
print version
Publication date 04.01.2007gg
Liked? Subscribe to RSS news! You can also support shram.kiev.ua, click:
Do not be amiss to your friends and find out this information, share with them the article!
|
Comments
Commenting, keep in mind that the content and the tone of your messages can hurt the feelings of real people, show respect and tolerance to his interlocutors, even if you do not share their opinion, your behavior in terms of freedom of speech and anonymity offered by the Internet, is changing not only virtual, but real world. All comments are hidden from the index, spam control.